
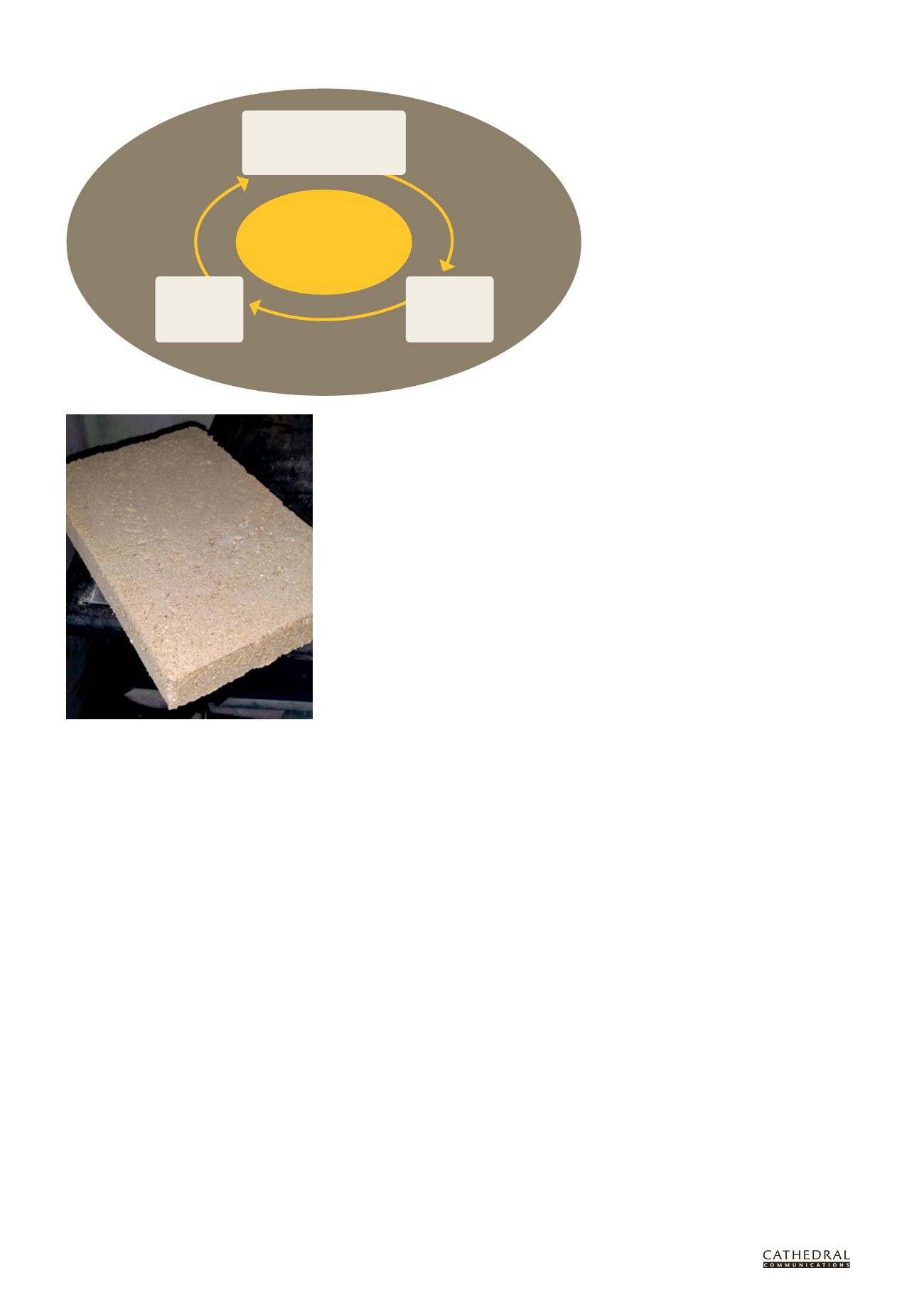
32
BCD SPECIAL REPORT ON
HERITAGE RETROFIT
FIRST ANNUAL EDITION
THE LIME CYCLE
as effectively as hydraulic lime but then
delivers the flexibility that is essential
for the conservation and repair of old
buildings. In one experiment, a piece
of carpet was skimmed with a plaster
made from this lime and allowed to set.
It did so overnight. It was possible to
dent the plaster with a thumb without
cracking it and even to bend the piece of
carpet without damaging the plaster. The
remaining mix from the experiment was
left in a tub. This same batch is now a hard
lump and the carpet plaster is still intact –
2½ years of poking and prodding, later.
DEVELOPING A LIME-BASED
INSULATION PRODUCT
In 2014 development of an insulation
system based on a non-hydraulic setting
mortar was awarded funding under
a Small Business Research Initiative
(SBRI) established by The City of
Cardiff Council, Cadw, Innovate UK
(formerly Technology Strategy Board)
and Low Carbon Trust with principal
funding from the Welsh Government.
The aim of the scheme was to assist the
development of ‘innovative measures
that will improve the energy performance
of traditional and historic buildings’.
The first step was to prepare sample
insulation panels (left) with a thickness
of 62mm (2½"). These contained Vivus
lime, mineralised wood chips and
various permeable aggregates selected
to ensure a very high degree of vapour
transfer, ideally suited to traditional
solid wall construction. Independent
testing confirmed thermal conductivity
of 0.1 W/mK in the least efficient sample
of Vivus render, in order to establish
a base-line, compared to 0.5 W/mK
typically found in conventional sand/
cement renders. (Thermal conductivity
is measured in watts per square metre of
surface area for a temperature gradient
of one kelvin for every metre thickness –
W/mK.) The tester also confirmed that
in his view even better results could be
expected if different aggregate materials
and thicknesses were used.
Currently the insulation systems in
common use are all impermeable and are
not readily compatible with older building
walls. The research confirmed that a
suitable insulation panel would be a useful
tool in the retrofit armoury.
Testing and experimentation is on-
going to determine exactly how thick the
panel or how deep the insulation needs
to be, to provide adequate insulation and
to buffer humidity, but without being too
deep to apply to older walls with existing
architectural features. Findings are
expected during the course of 2017.
Other materials such as plasters and
renders were also developed using the
same quick setting non-hydraulic lime
and a similar range of aggregates. During
workshop trials these were shown to be
successful in their ability to set and, once
dry, in their ability to absorb and readily
release humidity. Conventional lime
sand mortars tend to have a much higher
degree of capillarity due to the impervious
nature of the mineral aggregate, drawing
moisture in and retaining it for longer, off-
setting some of the benefits of the lime.
The advantage of a premixed product
using carefully selected aggregates is that
the resulting render, plaster or insulation
panel is able to work in a diffusive manner,
without capillarity.
The plasters and renders also work in
conjunction with the insulation material
to create a holistic approach to insulating
and finishing historic buildings. The
materials are all compatible with those
found in older buildings. The panels
are best fitted to either internal or
external faces of exterior walls by being
solid bedded onto the surface using
the non-hydraulic setting lime mortar.
The reasoning is that the panel will
then become an integral part of the
wall, thus ensuring the original design
is maintained, promoting seamless
humidity extraction through the
structure. This simple approach contrasts
with many modern retrofit solutions
which include air-gaps, capillarity and
impervious layers.
MANUFACTURING AND TESTING
Following successful completion of the
insulation tests, the product was approved
for a second phase of SBRI funding.
£142,000 was awarded for developing
commercial production, for developing
variations in the setting time, and for
demonstrating the products in a ‘whole
house project’.
The facilities of a manufacturing
company in Derbyshire were used
to test production of the material
in normal commercial mixing and
blending apparatus, and to benchmark a
manufacturing process and ability.
Due to the high temperature of the
chemical reaction (approaching 200°C
during slaking), it very quickly became
obvious that specialist machinery
would need to be developed in order to
manufacture the binders if they were
to ever reach the market. Nevertheless,
enough materials were produced for
demonstrating the product. The first
successful prototype machine is now in
operation, with basic materials being
produced in autumn 2016.
The house chosen for the ‘whole
house’ demonstration was Mill Cottage, in
Pontcanna, Cardiff, which was saturated
and rotting before the works began.
The house is of 18th-century origin with
19th-century rebuilds. As with many
One of the pre-production insulation panels tested,
62mm (2½
"
) thick
FIGURE 1
CARBONATION
Carbon dioxide (CO
2
)
slowly absorbed
from the air causing
the lime to set
FIRING
At high temperature, crushed
chalk or limestone (calcium
carbonate) turns to quicklime
and carbon dioxide
SLAKING
Water is added to the
quicklime producing a
violent reaction generating
heat and steam (if the
quicklime is mixed with
aggregate before slaking,
this is said to be a ‘hot
mixed’ mortar)
Calcium hydroxide (CaOH)
‘Lime’ – often referred to as
air lime, non-hydraulic lime,
lime putty, or if dried, as
‘hydrated’ lime
Calcium
carbonate
(CaCo
4
)
eg limestone
or chalk
Calcium oxide
(CaO)
‘Quicklime’